Das Anfertigen von Schwungmassen
So eine
Schwungmasse sieht recht einfach aus, ist ja eigentlich nur ein
Stückchen Rundmaterial mit Loch, muß aber doch ebenso genau
gefertigt werden wie ein Rad. Die an der Motorwelle auftretenden
Umdrehungen pro Minute sind doch deutlich höher als am Rad und
kleinste Ungenauigkeiten führen zu einer Unwucht, die zum
"Schlagen" der Schwungmasse führt. Das äußert sich in
einem
merklichen Zittern der Lokomotive und in deutlich hörbaren
Geräuschen.
Das grundsätzliche Problem sind die Rundlauf-Ungenauigkeiten der
normalen Drehmaschinen, jedes Umspannen bringt neue Unwucht, deshalb
sollte die potentielle Schwungmasse nicht umgespannt werden und in
einem Durchgang gefertigt werden.
Grob unterteilt gibt es zwei Arten von Schwungmassen, jene, die auf
ausreichend lange Motorwellen aufgesteckt werden und sich dann zwischen
Motorlager und Mitnehmer oder Zahnrad/Schnecke sitzen und die,
die wegen zu kurzer Motorwelle auf einer Seite die
Aufnahmemöglichkeit für die Kardanwelle o.ä. haben
müssen. Diese kann ebenfalls gedreht werden, ich bevorzuge aber,
nach einiger Erfahrung, "durchbohrte" Schwungmassen und stecke lieber
eine Welle ein, als einen Zapfen zu drehen.
Zur besseren Wirkung sollten Schwungmassen so groß wie
möglich ausgeführt werden. Eine Daumenregel sagt, eine vom
Durchmesser verdoppelte Schwungmasse hat die gleiche Wirkung wie eine
auf die vierfache Länge gebrachte Schwungmasse mit dem
angenommenen Durchmesser 1.
|
|
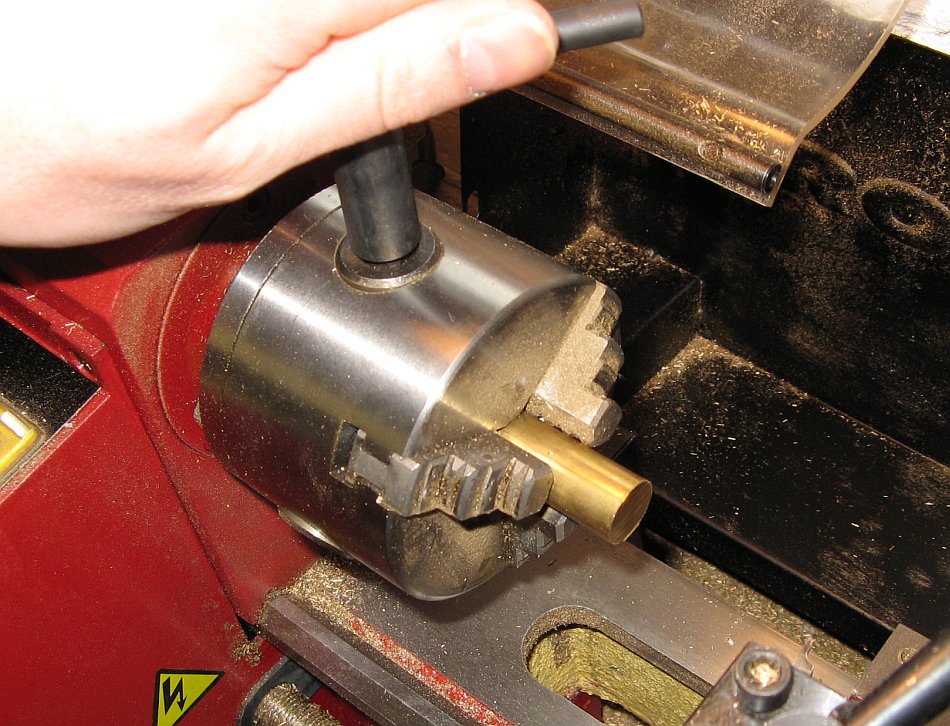
Bild 1
Einspannen des Rundmaterials.
|
Das
Rohmaterial, gewöhnlich Messing-Rundmaterial (Modulor (geht so)
oder Conrad (sauteuer) wird eingespannt. Da Messing recht weich ist,
sollte man das Material kurz einspannen. sonst kann es passieren,
daß unter dem Druck des Drehmeißels das Material an den
Backen nachgibt.
Nach dem Einspannen sieht man u.U. schon, wie der Stab schlägt.
Zuerst wird, wie in meinem Falle, von neuem Material die gesägte
und schiefe Stirnseite abgestochen. |
|
|
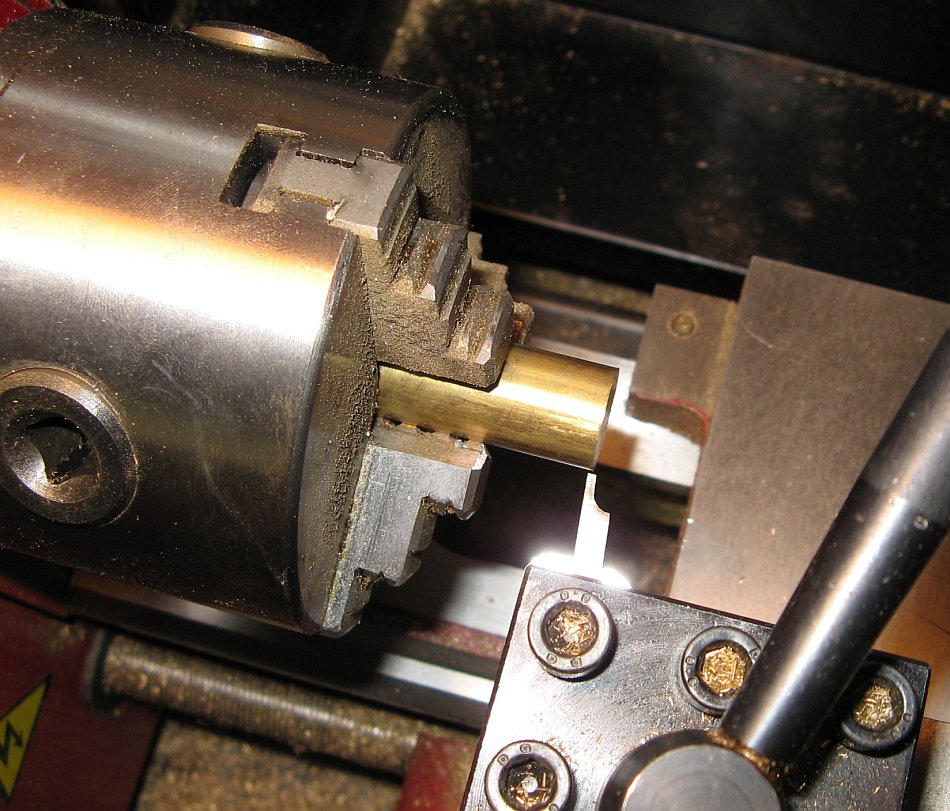
Bild 2
Das Rohmaterial vorn Abstechen.
|
Auf dem folgenden
Bild kann man recht gut den selbstgeschliffenen Meißel erkennen.
Durch seine geringen Abmessungen würde benötigt er eine Reihe
Unterlagen, um auch in der richtigen Höhe zu sitzen, damit in
Futterlängsachse kein Material stehen bleibt.
|
|
|
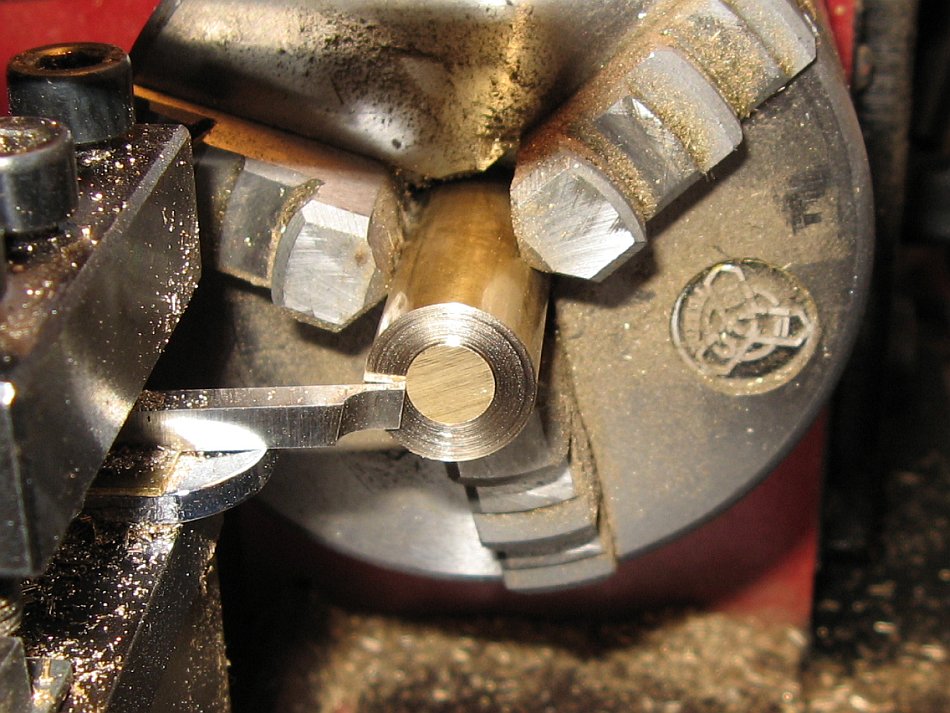
Bild 3
Das Abstechen.
|
Dann
wird die durchgehende
Bohrung vorbereitet. Dafür nutzt man eine Zentrierbohrer, den das
folgende Bild zeigt.
|
|
|

Bild 4
Der Zentrierbohrer im Futter des Reitstockes.
|
Der
Reitstock ist gerade bei Heimwerkergeräten nicht so 100%ig
perfekt. Einige Besitzer klagen über einen Höhenversatz, bei
mir war es im Lieferzustand ein seitlicher Versatz von rund 1,3 mm. Das
sollte deshalb vorher überprüft und so weit möglich
korrigiert werden. Exakt wird man das kaum hinbekommen, deshalb der
Hinweis, das Bohrfutter des Reitstockes möglichst weiter raus
zudrehen, um durch das zusätzliche Spiel den Bohrern die
Möglichkeit zu geben, durch Verbiegung den Versatz auszugleichen.
|
|
|
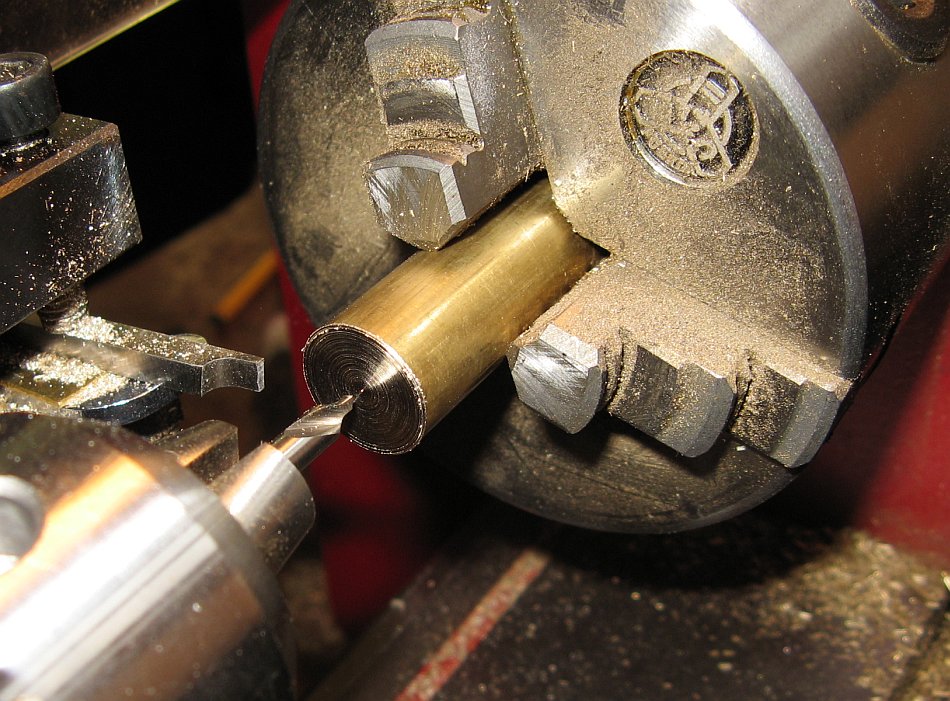
Bild 5
Der Zentrierbohrer kurz vor dem Ansetzen.
|
Nach
dem Setzen der Zentrierbohrung wird die Bohrung für die Motorwelle
mit minimalem Untermaß eingebracht. Für die üblichen
Wellen mit 2 mm Durchmesser sind 1,95 mm eine gute Wahl. Fehlt ein
solcher Bohrer, sollten nicht 1,9 oder gar 1,8 mm gebohrt werden. Da
bekommt man nie eine Welle rein und wenn, dann nur unter Inkaufnahme
von Schäden oder Unwucht. Dann lieber 2 mm bohren und die
Schwungmasse mit Sekundenkleber sichern. Das hält bei mir
bombenfest.
Benutzen Sie "Bohr- und Schneidöl" um ein Abbrechen des recht
kleinen Bohrers zu verhindern. Lieber öfter den Bohrer wieder
rauskurbeln und von Spänen befreien, als in einem Zug durchbohren.
Bohren Sie tiefer als die Dicke der Schwungmasse betragen soll!
Nachbohren ist kein guter Vorschlag. Einmal wird die Oberfläche
der Schwungmasse durch das Backenfutter verändert, was zu einer
Unwucht führen kann. Zum anderen ist nicht garantiert, daß
beim Nachbohren die vorhandene Aufnahmebohrung nicht verändert
wird.
|
|
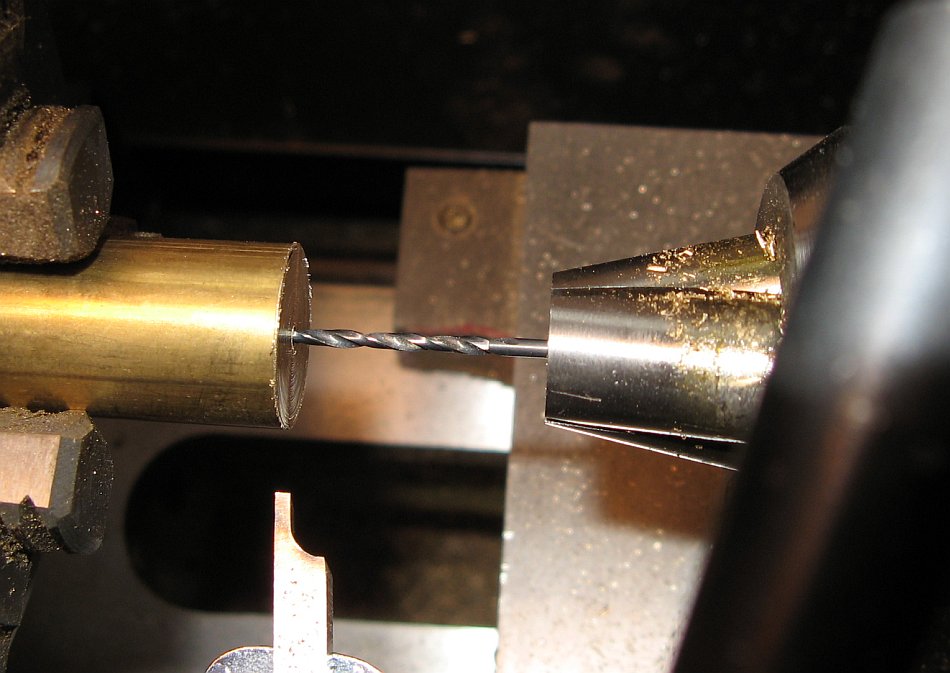
Bild 6
Das Bohren der Wellenaufnahme.
|
Ist
die Bohrung fertig, wird die zukünftige Schwungmasse
überdreht. Dabei sparsam rangehen, immer nur wenige hundertstel mm
überdrehen, bis die Oberfläche vollkommen gleich aussieht.
Will sagen, die angelaufene Oberfläche um komplett runter. wo sie
noch sichtbar ist, hat die Schwungmasse Untermaß.
Dann messe ich die Dicke der Schwungmasse und setze mit einem
Abstecher genau am Ende an. Bis etwa zur Hälfte stecke ich die Nut
ein, dann werden die Kanten an der Schwungmasse bei Bedarf (wenn zu
scharf) gebrochen und mitunter poliere ich die Oberfläche auch.
Arbeitsschutzhinweis:
Kanten brechen sollte mit einem eingespannten Drehmeißel und
nicht mit einer Schlüsselfeile erfolgen. Eigentlich sollte das
klar sein, den wenn der Bediener abrutscht, gerät das Werkzeug
u.U. in das Backenfutter, wird aus der Hand geschlagen und fliegt mit
Wucht durch den Raum. Also: Kein Leichtsinn!
Auch das Polieren mit in der Hand gehaltenem Sandpapier o.ä. bei
laufender Maschine verstößt gegen sämtliche
Arbeitsschutzregeln. Auch dafür gibt es geeignete Werkzeuge. Wenn
ein Finger vom laufenden Backenfutter erfaßt wird, ist das nicht
nur sehr schmerzhaft, die folgende Verletzungen sorgen auch dafür,
daß mit mit dem Modellbau erst einmal pausiert werden muß.
|
|
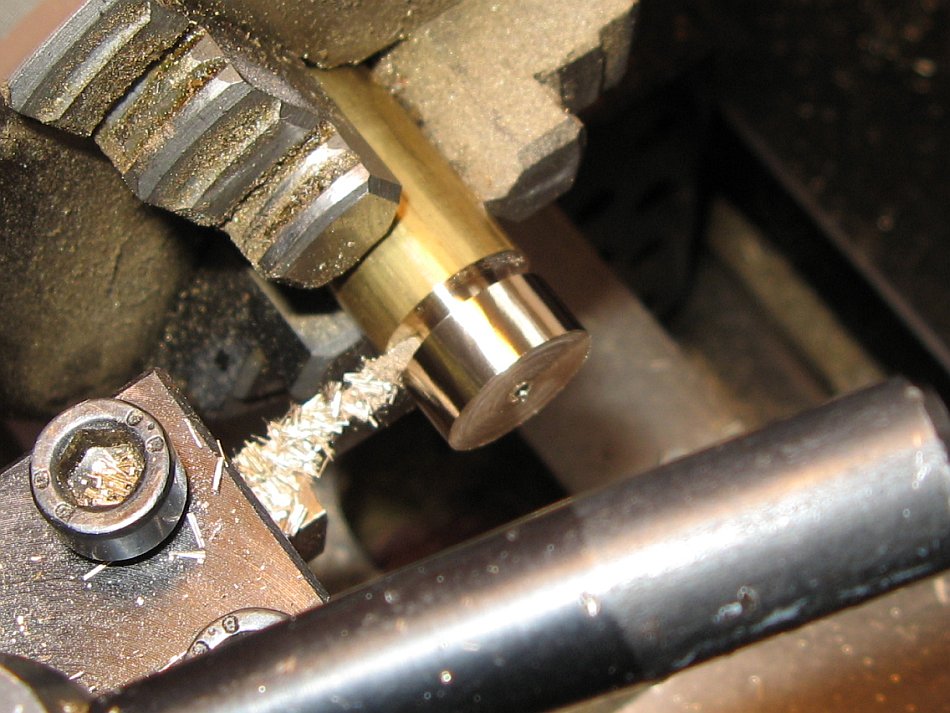
Bild 7
Einstechen der Nut...
|
Das
Abstechen ist nun kein Akt mehr, man sollte nur darauf achten,
daß die fertige Schwungmasse nicht unglücklich fällt
und dabei Dellen und Kerben bekommt. Stichwort: Unwucht. |
|
Bild 8
...und das Abstechen aus einer anderen Perspektive.
|
Abschließende
Arbeiten:
Bei Bedarf müssen
die Bohrungen nun noch mit der Hand entgratet werden. Dann wird eine
Welle (ich benutze dafür Wagenachsen alter Piko-Radsätze, mit
2 mm Durchmesser) bis zur Hälfte eingesetzt. Die Motorwelle
muß bei Bedarf abgeflext werden, dann wird die Schwungmasse auf
gesetzt und bei Bedarf gesichert.
Wenn man sauber
gearbeitet hat, zeigen weder Schwungmasse noch der eingesetzte
Wellenstumpf beim Probelauf eine Unwucht.
|
|